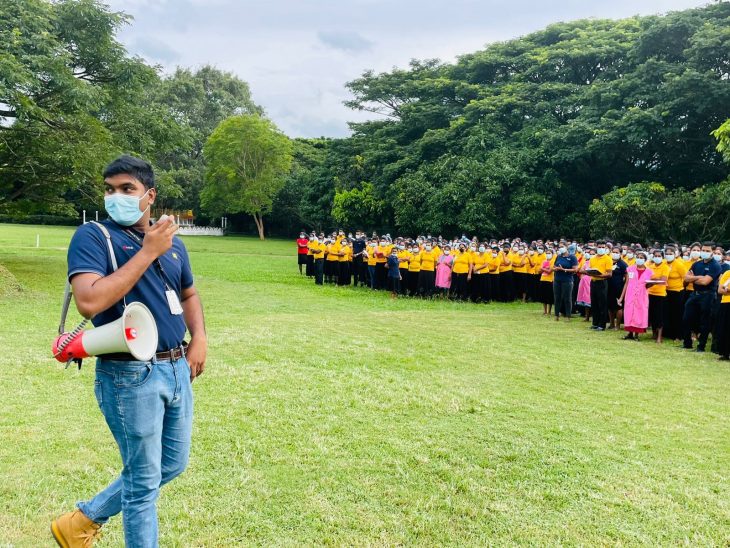
Compliance, Health & Safety Aspects in Apparel Industry
Vol 26, Issue 14
Now-a-days, there is a major focus on the compliance, health, and safety adherence in the apparel industry, rather than just focusing on apparel manufacturing. Famous brands such as Nike, Adidas, Zara, Calvin Klein, Tommy Hilfiger, Patagonia, and others have increased their attention towards more ethical and sustainable manufacturing practices which driven by a commitment to compliance and health and safety standards. While some industries may segregate these aspects, the apparel industry is currently seeming to be combining the compliance, health & safety due to their link to each factor.
When look at compliance requirements, brands are more conscious on labour standards within their manufacturing facilities. Fair wages, appropriate working hours, the eradication of child labour, the promotion of freedom of association, the prohibition of forced labour, non-discrimination practices, and the prevention of harassment are some of them. The World Wide Responsible Accredited Production (WRAP) has introduced 12 principles that directly address key aspects of these compliance requirements. At the moment, a considerable amount of of apparel brands follow WRAP certification as a guiding tool for their own compliance standards. Based on their own criteria, brands are typically undertaking annual or bi-annual audits to assess the compliance, health & safety status of their manufacturing facilities. Additionally, there are more guidelines such as Custom-Trade Partnership Against Terrorism (CTPAT) which helps to ensure the security and privacy of supply chains. When we focus on health and safety, the apparel industry has placed a significant emphasis on machinery safety, given the extensive use of machinery in day-to-day production processes. The primary focus lies in accident prevention, which is achieved through machinery guarding and regular maintenance protocols. Workforce training programs are implemented regularly to boost awareness of workplace safety. Chemical management is a crucial aspect of health and safety considerations, given the numerous uses of various chemicals in the industry, particularly in dyeing, spot cleaning, and washing departments. It is essential to equip personnel in these departments with appropriate safety gear, including eye guards, gloves, face masks, and aprons. Fire safety emerges as another focal point within the health and safety framework. Organizations diligently conduct mock drills, assess and service fire equipment, perform compatibility tests, and undertake evaluations to mitigate potential fire risks, recognizing the catastrophic consequences of unmitigated incidents. Moreover, first aid training programs are systematically conducted to ensure a prompt and effective response in emergency situations. International standards require distinctive headcount ratios to maintain a trained workforce for firefighting and first aid teams, aligning with comprehensive safety protocols.
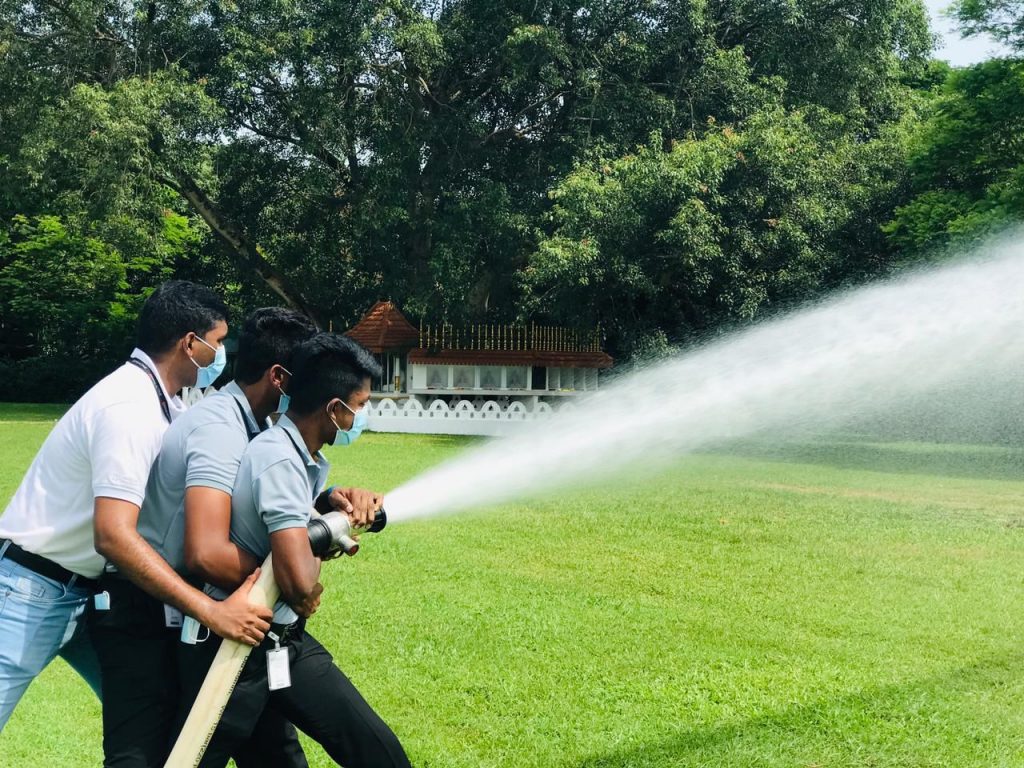
In addition to the above-mentioned points, apparel companies also adhere to compliance, health, and safety standards. It is clear that these companies prioritize compliance, health, and safety factors to a great extent, with the aim of ensuring sustainable outcomes and implementing better practices within their factory premises.
- Sri Lankan Universities – Student Story - 19th April 2024
- Winter Experience – Student Review - 12th April 2024
- Sushi – A work of art in the culinary world - 5th April 2024